锤式破碎机锤头耐磨新材料的研制
- 字号 + -
1 引言
锤式破碎机的锤头是破碎机的主要易损件,每年要消耗大量的金属材料。目前国内的破碎机锤头大部分使用高锰钢材质,使用寿命非常短,而且出机物料由于锤头的磨损过快造成篦条和锤头的间隙过大而粒度不均匀,影响下一步的粉磨过程,同时频繁停机更换锤头增加了维修工作量,影响正常生产。如果锤头的硬度过高,在大块物料的打击下很容易造成锤头的断裂,不及时停机会造成设备事故。因此,研制出一种高强韧材质制作锤头具有十分重要的意义。
2 破碎机锤头的失效分析及对耐磨材料的性能要求
2.1 锤头的失效分析
锤式破碎机的工作简图见图1,物料从喂料口落下进入破碎腔,与高速旋转的锤头相撞击而被破碎。破碎后的物料落在有一定间隙的篦条上。这时锤头除了在破碎腔上部与继续落下的物料相撞击外,还要对破碎腔底部堆积在篦条上的物料施以撞击、碾压,迫使被破碎后符合要求的细小物料通过篦条卸出。在上述过程中,锤头除受到撞击外,还受到物料的冲刷。随着上述过程的不断重复,久而久之,锤头的原工作面遭到破坏,其表面形状发生了变化,原来的棱角磨削为光滑的圆弧面,见图2。从图2我们可以看到,作用在锤头磨面的力F分解为两个力,一是垂直于磨面的法向力F法;另一是平行于磨面的切向力F切。前者对锤头磨面产生撞击作用;后者对锤头磨面造成切削、冲刷。
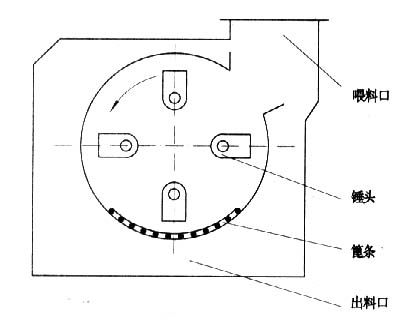
图1 破碎机简图
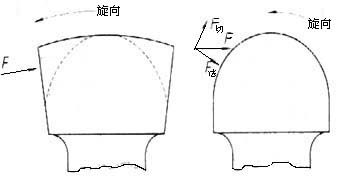
图2 锤头磨损前、后示意图
由锤头工作示意图和扫描电镜分析可知,破碎机锤头在工作中受到几种形式的磨损。在锤头工作初期其表面形状未发生改变时,锤头主要受到撞击磨损,物料以正向力撞击金属表面产生塑性变形和撞击坑。
当锤头的工作面磨损为弧面后,其表面的受力发生了变化,物料以一定的冲击角撞击工作面。此时锤头除了受到物料以正向力F法的撞击磨损外,还受到物料对它的冲刷造成的犁削。当材料硬度较低时物料刺入其表面,在水平分力F切的作用下将材料推至两侧,造成堆积和隆起,形成犁沟;而材料硬度较高时,磨损过程则以切削材料为主。被切削的材料一部分呈磨屑流失,另一部分尚与母体连接的磨屑经再次切削和冲击后终还是断裂脱落。同时在物料的反复多次冲击下,冲击坑的翻边和犁沟降起的两侧因多次变形脆化而产生裂纹。裂纹经连接和扩展后产生了疲劳剥落。由于高锰钢锤头硬度低,不能有效地抵抗物料的刺入和刻划,因而造成严重的犁沟和犁削,使其表面磨损加速。尽管物料的撞击可产生一定量的加工硬化,但冲击力还不足以使锤头的工作面形成坚固的硬化层,造成锤头的耐磨性不够,终导致短期失效。因此提高锤头材质的硬度必然有助于其耐磨性的提高,可使物料对金属表面的犁削现象减轻。提高材质的韧性可以抑制裂纹的萌生和扩展,有助于减少疲劳剥落的形成,从而提高耐磨性。
2.2 锤头材质应具备的性能要求
材料的硬度是影响其耐磨性的一个重要因素。物料与耐磨材料的硬度比值Ha/Hm对磨损率有很大影响。当0.7≤Ha/Hm≤1.3时,磨损率开始上升,耐磨性降低,如图3所示。
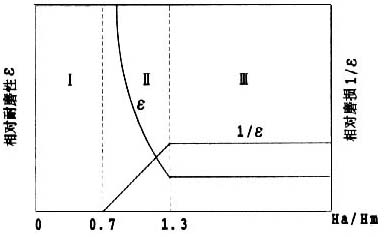
图3 相对磨损、相对耐磨性与Ha/Hm的关系
这时如物料硬度不变,设法提高金属材料的硬度以使其耐磨性显著提高。水泥生产中硬的物料为水泥熟料,其硬度在HB480左右。因此在破碎熟料时要想得到较低的磨损率,就必须将锤头的硬度提高到HB460(HRC49)以上。这是确保破碎机锤头工作时具有高耐磨性的根本条件。高锰钢的硬度远远低于上述值。对从现场取回的高锰钢锤头残体进行了多次测试,其结果表面硬度只有HB230~350(HRC21~38)。说明预期的加工硬化效果没有达到,从而硬度很低。这个硬度值对于破碎水泥熟料属于硬磨料磨损,因而工件磨损严重而早期失效。
当然一味地提高材料的硬度并不一定就能提高材料的耐磨性。金属材料的耐磨性是个综合因素指标,与材料的硬度和韧性都有密切的关系,韧性对提高材料的耐磨性有着不可忽视的作用,韧性是材料本身吸收外部能量大小的标志,这对于在有冲击载荷的磨损工况下显得十分重要。高铬铸铁是一种的耐磨材料,但是用它制作破碎机锤头的欠缺处就是韧性偏低,易发生断裂。生产实践证明了材料硬度相同,而冲击韧性不同的锤头,其耐磨性是随冲击韧性值升高而增加的,即αk值高,使用寿命长。同时实践证明,制造破碎机锤头的材质其冲击韧性应大于10J/cm2。
3 材质化学成分的确定
高碳可以获得较高硬度基体,同时产生一定数量的碳化物硬相来抵抗硬质物料磨损。铬、镍、钼元素的配合加入强烈地提高钢的淬透性,使工件在空冷状况下也能淬成马氏体。这对生产中热处理工艺的制定具有较大的实际意义,而镍同时可使钢的韧性—脆性转变温度降低,提高钢的韧性,有益于在实际工况中受冲击载荷的工件。少量的钛和稀土元素可细化晶粒,净化晶界,提高钢的强度,见表1。
4 试验方法
4.1 试样制备
采用30kg碱性中频炉熔炼浇注成梅花试样,按标准加工成各项试验所需尺寸,冲击为10mm×10mm×55mm无缺口试样。
4.2 试验设备、仪器
硬度测试采用HR—150A洛氏硬度计;冲击韧性试验采用F—30B重摆锤式冲击试验机;拉伸试验在WE—60材料试验机上进行。磨损试验在MLD—10动载磨料磨损试验机上进行,试验参数为:冲击功1J、3J;冲击频率100次/min;磨料为5~10目石英砂;磨料流量为30kg/h;冲击时间0.5h。
4.3 显微组织分析
用XJG—05型卧式光学显微镜进行金相检验;高倍分析在CAMEBAX—MICRO大型电子摆针上进行,以获得研究材料的高倍电子扫描图像及各元素的分布情况。
5 试验结果分析
5.1 硬度和韧性对耐磨材料的影响
为了使试验钢有一个冲击韧性与硬度的佳配合,我们设计了900℃、940℃、980℃三种淬火温度和五种回火温度,以寻求合理的热处理工艺(见表2)。
图4显示了淬火温度与硬度的关系。可见随着淬火温度的提高,硬度不断提高。在930℃和950℃之间硬度出现峰值,之后温度再提高,硬度趋于下降。比较表2中试验钢在各热处理状态下的性能,可以看出在940℃淬火时钢的综合机械性能优于900℃、980℃淬火时的机械性能。图5显示了回火温度对试验钢的硬度、强度和冲击韧性的影响。随着回火温度的提高,硬度缓慢下降,当回火温度至400℃时,由于合金元素的沉淀硬化,硬度略有回升,在450℃上下保持有较高的硬度。继续提高回火温度,马氏体中碳的过饱和度降低,使得硬度降低。但回火温度在500℃时仍能保持在HRC50以上,说明此钢有较好的回火稳定性。由于淬火钢中有较大的残余应力,故淬火态的强度低。随着回火温度的升高,残余应力逐渐消除而使强度上升,升至300℃左右出现峰值,继续提高回火温度,强度开始下降。冲击韧性的变化是随着回火温度的提高冲击值呈上升的趋势,在280℃冲击值开始降低,出现了回火脆性,继续提高回火温度至400℃以后,冲击值又恢复上升。
表2 试验钢的热处理和性能
编号热处理状态(皆为空淬)HRCαk(J/cm2)组织
1900℃淬火,不回火54.49.3M+K+A′
2900℃淬,280℃回52.615.2M回+K+A′
3900℃淬,350℃回52.112.9M回+K+A′
4900℃淬,420℃回52.913.5M回+K+A′
5900℃淬,480℃回51.816.8M回+T回+K
6900℃淬,540℃回48.721.7T回+K
7940℃淬火,不回火57.58.9M+K+A′
8940℃淬,280℃回53.415.9M回+K+A′
9940℃淬,350℃回53.012.4M回+K+A′
10940℃淬,420℃回54.413.6M回+K+A′
11940℃淬,480℃回52.817.1M回+T回+A′
12940℃淬,540℃回50.722.3T回+K
13980℃淬火,不回火56.29.8M+K+A′
14980℃淬,280℃回53.116.2M回+K+A′
15980℃淬,350℃回52.612.7M回+K+A′
16980℃淬,420℃回54.113.9M回+K+A′
17980℃淬,480℃回52.917.6M回+T回+K
18980℃淬,540℃回51.122.9T回+K
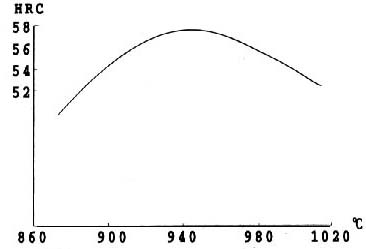
图4 淬火温度与硬度的关系
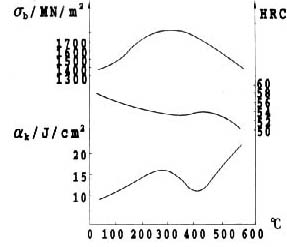
图5 回火温度与机械性能的关系
表3 磨损试验结果
冲击功(J)编号失重(g/h)相对
耐磨性
第一次第二次第三次平均
1100.1650.1570.1610.1612.83
110.1670.1650.1700.1672.73
Mn130.4550.4610.4520.4561
3100.1680.1760.1730.1722.45
110.1640.1590.1600.1612.61
Mn130.4140.4230.4280.4211
表3得出了在不同冲击功下高锰钢和铬镍钢的磨损试验结果。可见高锰钢在较高的冲击功下的磨损量比在低冲击功时的磨损量小,耐磨性有所提高,这可能是加工硬化所致。而铬镍钢硬度较高的10号试样在低冲击功下的磨损量小于硬度低而韧性稍高的11号试样。在较高冲击功下恰恰相反。这说明低冲击应力下的冲击磨损耐磨性取决于硬度指标;而较高冲击应力下的冲击磨损耐磨性取决于韧性和硬度的综合指标。
为了描述硬度、冲击韧性和磨损量之间的关系,我们选取一些锤头材质试样,测定其硬度、冲击值,再做动载磨损试验,测出其磨损失重,得出各种材质的三个参数数据。磨损量、硬度和冲击韧性之间存在的关系式为:
Y=b0+b1x1+b2x2 (1)
式中:Y——磨损量,g/h;
x1———冲击韧性,J/cm2;
x2———硬度,HRC。
通过回归分析得出回归方程:
Y=1.19-0.035x1-0.018x2 (2)
利用以上回归方程,绘出各种韧性条件下硬度与磨损量之间的关系,见图6。
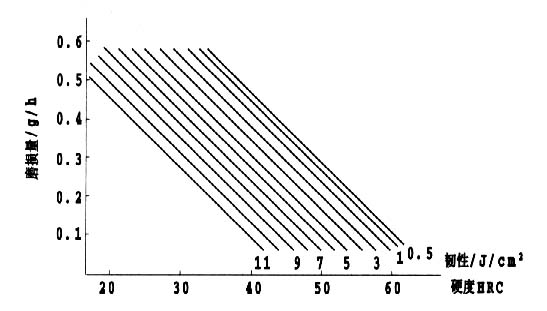
图6 磨损量与硬度、韧性的关系
图6显示高硬度、高韧性的材料磨损量少,但一般情况下材料的硬度和韧性密切相关,韧性高时硬度较低,硬度高时韧性又较低(少数合金钢除外)。因此必须考虑它们对磨损量的综合影响。由于锤头工作时承受冲击载荷,为了避免冲击断裂选材时在有高硬度的前提下,尽可能的选择冲击韧性的大值。这样既可避免冲击断裂,又可以使磨损量较小,从而提高锤头的耐磨性。
5.2 显微组织对耐磨性的影响
材料的耐磨性和其组织有着密切的关系。磨损试验表明材料的耐磨性首先取决于组织。硬度是材料抵抗物料压入表面的能力,硬度高物料压入材料表面的深度就浅,切削产生的磨屑体积小,即磨损小,耐磨性高。韧性高说明材料可吸收的能量大,裂纹不易形成和扩展,材料承受反复变形能力大,不易形成疲劳剥落,即耐磨性高。试验表明,硬度相同的不同材料其耐磨性是有差异的。同样,韧性相同的不同材料耐磨性也不相同。如淬火态的试样和淬火+回火的试样相比较,硬度可能相当,但由于韧性不同而造成耐磨性不同。其实质是显微组织的不同而造成的耐磨性不同。但如果钢的显微组织相同,可以以硬度的高低衡量耐磨性的高低。图7反映了合金钢基体组织和耐磨性的关系,可见回火马氏体和贝氏体具有较高的耐磨性。试验的铬镍钼钢经淬火、回火处理后,金相组织为:回火马氏体+弥散分布的碳化物。其硬度为HRC54,冲击韧性为16J/cm2,具有较高的综合机械性能。
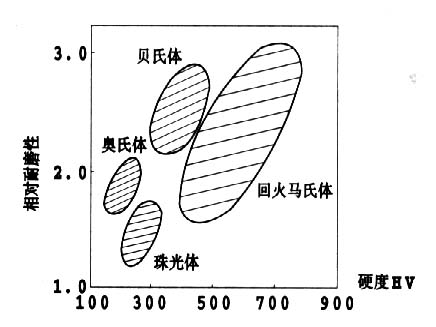
图7 钢的组织与耐磨性的关系
6 生产试制及装机试验
在实验室研制的基础上我们在铸造厂生产了部分铬镍锤头产品,在水泥厂作进一步装机试验。熔炼在500kg中频电炉中完成,熔炼温度1530~1580℃,浇注温度1420~1480℃。稀土合金冲包熔化,然后扒渣浇注。木模收缩率按2%,造型采用糖浆砂,表面烘干,型腔刷涂料,工作面加外冷铁,以求获得细晶粒、无砂眼、无气孔的高质量铸件。铸件浇冒口应用锤敲下,尽可能不用气割,以防裂纹产生。铸件热处理在台车式电阻炉中完成,为防止加热速度过快产生开裂,升温速度控制在≤150℃/h,在750℃保温2h,然后随炉升温至淬火温度,保温0.5h后风冷,淬火后的锤头堆积在一起自回火,再送入炉中回火,回火后出炉应快冷,以防止回火脆性产生。
1993年10月~1995年7月铬镍钢锤头分别在江苏省仪征水泥厂Φ800mm×600mm锤式破碎机、江苏省金坛县第二水泥厂Φ800mm×400mm锤式破碎机、安徽胜利水泥厂750—4型立轴式破碎机、山东省淄博淄川水泥厂Φ800mm×600mm锤式破碎机上装机试验,并同机装入高锰钢锤头同时使用。试验结果表明:铬镍钢锤头使用寿命是高锰钢锤头的2.8至4.3倍,锤头在使用过程中未发生过断裂现象。
7 经济效益
铬镍钢锤头的价格虽是高锰钢的1.29倍,而其耐磨性平均是高锰钢的3倍。因此综合计算,前者只是后者消耗量的0.43倍,即用铬镍钢锤头可节约资金57%。如铬镍钢锤头在100家水泥厂推广使用,每年可节约资金300多万元。
新动态
-
2024-12-03
制砂机润滑失效有哪些原因?
-
2024-12-02
破碎石子的设备有哪些,一台多少钱?
-
2024-11-30
时产300吨石英机制砂生产线如何配置
-
2024-11-29
石料厂石头打成沙子需要用到哪些设备?
-
2024-11-28
锰矿石破碎工艺及破碎加工生产线案例
-
2024-11-28
建筑用石料和机制砂粒径划分标准
-
2024-11-27
时产300吨移动破碎站适用哪些行业?
-
2024-11-26
冲击破与圆锥破哪种破碎鹅卵石效果好?
-
2024-11-25
大型石子生产线运行时如何解决破碎机堵料问题?
-
2024-11-23
矿石加工生产线运行时颚式破碎机偏心轴弯曲如何解决?